Introduction to Kaizen and Its 10 Principles
A Gentle Introduction to Kaizen
In the bustling world of organizational management and development, there lies a serene yet potent philosophy that has revolutionized the way businesses operate. Welcome to the realm of Kaizen. Originating from Japan, the term ‘Kaizen’ gently unfolds into ‘Kai’ meaning change, and ‘Zen’ signifying goodness or betterment. In essence, Kaizen isn’t merely a methodology; it’s a philosophy that embraces continuous, incremental improvement in every facet of life, be it personal, social, or professional.
The Quintessence of Continuous Improvement
Imagine a river, perpetually flowing, incessantly finding new paths, and gracefully adapting to the terrains it traverses. Kaizen, in the organizational context, mirrors this natural phenomenon. It’s not about abrupt, radical changes but about fostering a culture where every cog in the organizational wheel, from the CEO to the janitor, is perpetually in a state of seeking and implementing small, consistent improvements. The beauty of continuous improvement lies in its subtlety and sustainability. It’s not about making massive leaps; it’s about taking mindful, deliberate steps that culminate into a journey towards operational excellence and customer satisfaction.
Unveiling the 10 Principles of Kaizen
Embarking on this journey requires more than just an understanding; it demands a structured approach, a roadmap that navigates through the various aspects of organizational functioning. Here, we introduce the “10 Principles of Kaizen,” a guide that illuminates the path towards continuous improvement in a harmonious, inclusive, and sustainable manner. These principles aren’t merely strategies; they are philosophies that permeate through the organizational fabric, ensuring that the pursuit of improvement is not a task but a culture.
In the Upcoming Journey…
As we delve deeper into each principle in the subsequent sections, we’ll explore not just their definitions, but their soul, their impact, and their practical applications in various organizational landscapes. From tales of global conglomerates to stories of small startups, the principles of Kaizen have painted every canvas with strokes of improvement, innovation, and incessant development.
The Essence of Kaizen: A Gentle Journey Through its Core
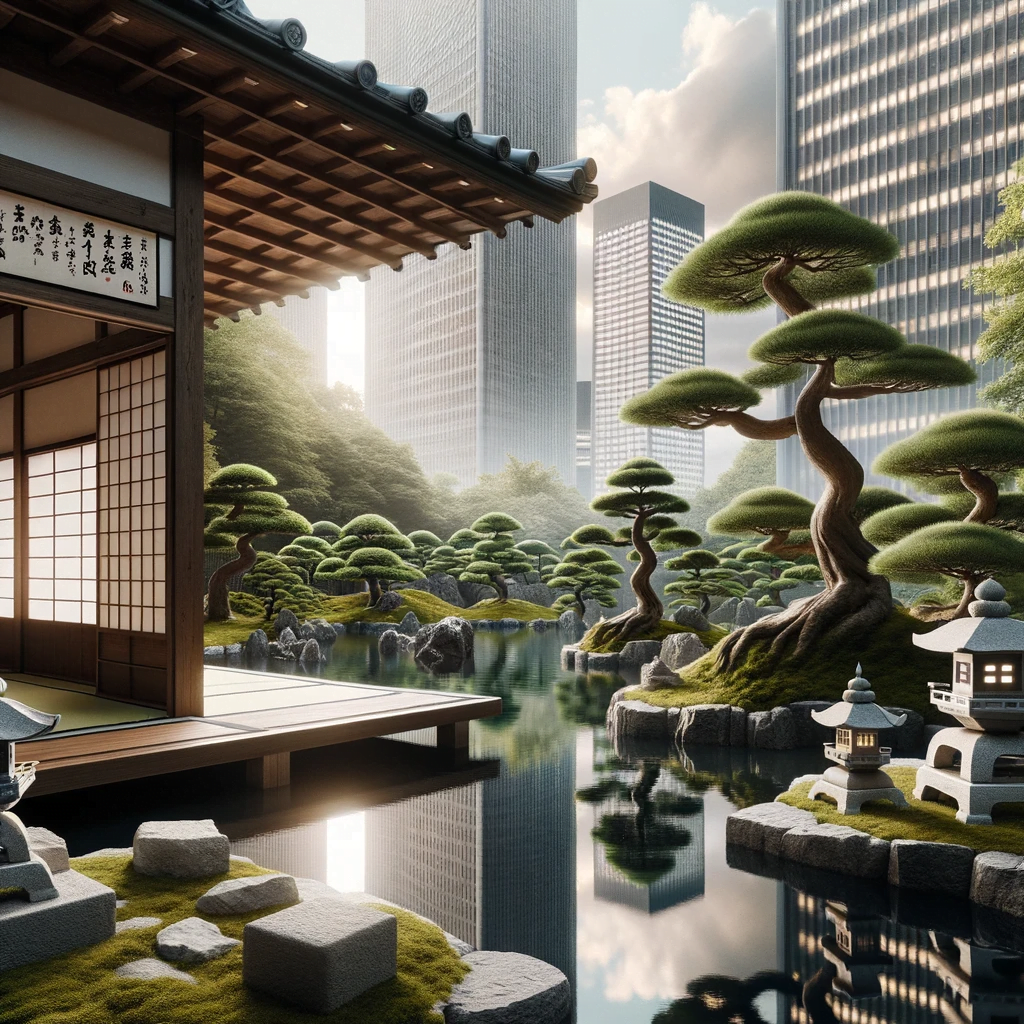
Defining Kaizen: A Beacon of Continuous Improvement
In the lush landscapes of organizational philosophies, Kaizen emerges, not as a mere strategy, but as a gentle breeze of perpetual enhancement and growth. The term ‘Kaizen’ blossoms from the Japanese words ‘Kai’ (change) and ‘Zen’ (good), seamlessly weaving into a philosophy that whispers the art of continuous improvement. It’s not a thunderous revolution but a subtle, ongoing evolution towards betterment, one small step at a time.
The Core Philosophy: A River of Unending Betterment
At its heart, Kaizen isn’t bound by the rigid walls of methodologies or strategies. It’s a philosophy, a mindset that permeates through every layer of an organization, gently nudging it towards a state of constant, never-ending improvement. Imagine a river, never stagnant, always finding new paths, adapting, and gently carving through landscapes to find its way. Kaizen is this river, flowing through an organization, softly eroding obstacles, and consistently moving towards a sea of improvement and efficiency.
Significance in the Modern Business Tapestry
In the modern business arena, where change is the only constant, Kaizen subtly intertwines with every function, quietly enhancing and improving. The “10 Principles of Kaizen” serve as the stepping stones that guide organizations through this gentle stream of continuous improvement, ensuring that every step taken is one towards betterment, efficiency, and growth. It’s not merely about fixing what’s broken but about consistently enhancing what works, ensuring that the organization is always on a path of improvement, always a step ahead, always evolving.
Principle 1: Improve Productivity – The Heartbeat of Kaizen
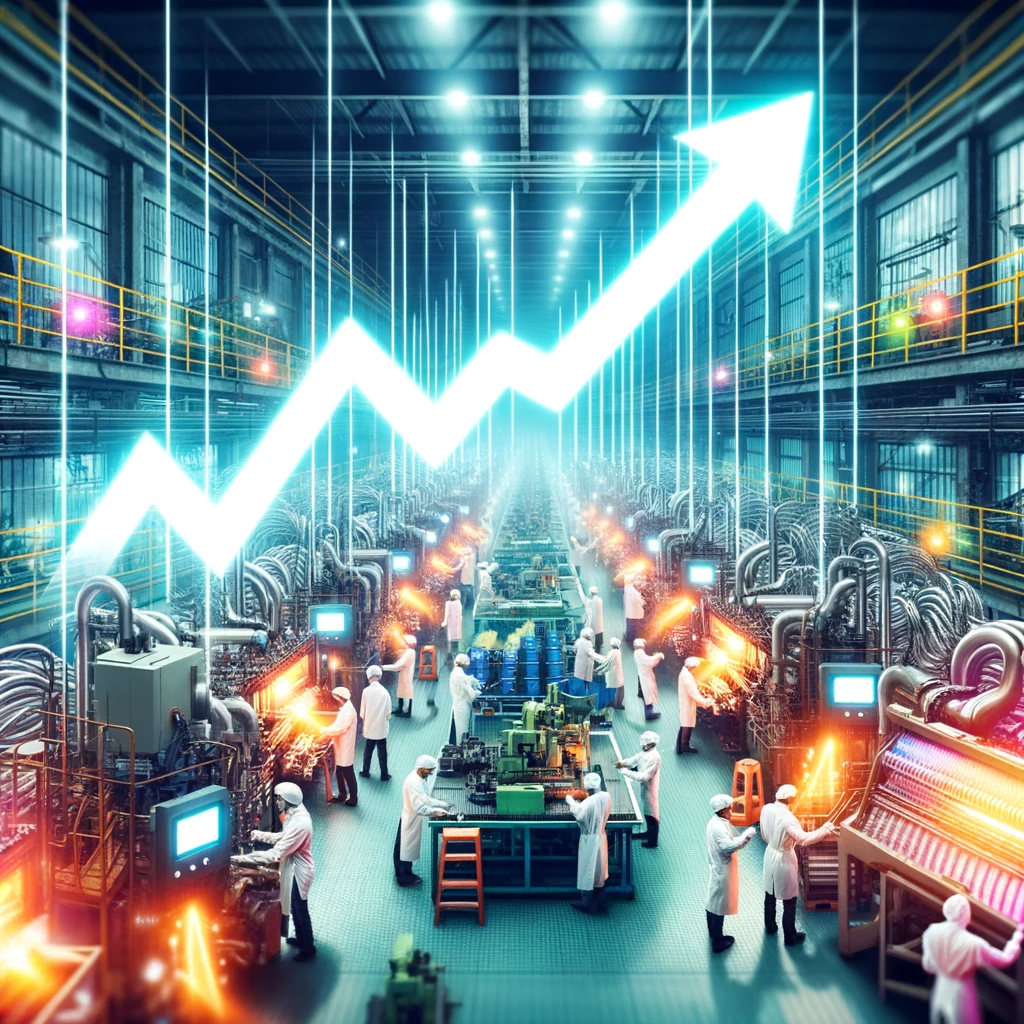
Defining Productivity in the Lens of Kaizen
In the enchanting journey through the “10 Principles of Kaizen,” the first principle gently whispers the essence of improving productivity. Productivity, in the Kaizen realm, isn’t merely a measure of output. It’s a harmonious melody that plays through every layer of an organization, ensuring that every note, every beat, and every rhythm is in a perpetual state of enhancement and refinement. It’s about ensuring that every resource, be it time, manpower, or material, is utilized to its utmost, ensuring a symphony of efficiency and effectiveness.
The Quintessential Role of Productivity
Imagine a garden where every drop of water, every ray of sunlight, and every nutrient in the soil is utilized to its fullest, ensuring that every bud blossoms and every leaf thrives. This is the role of productivity in Kaizen. It’s not merely about doing more; it’s about blossoming fully, ensuring that every action, every process, and every resource is optimized, ensuring a lush, thriving organizational landscape. It’s about ensuring that no drop of effort is wasted, that every action is a step towards organizational blossoming.
Embarking on Real-world Applications
In the real-world canvas, the principle of improving productivity paints every corner of organizational operations. Take Toyota, for instance. The automobile giant didn’t just implement productivity; they embraced it, ensuring that every process, every operation, and every action was a step towards enhanced productivity. Through meticulous planning, continuous improvement, and an unyielding commitment to ensuring optimal utilization of every resource, Toyota not only enhanced their productivity but also crafted a legacy that is often cited in the annals of organizational management and development.
Case Study: The Toyota Production System
The Toyota Production System (TPS), often hailed as the epitome of productivity, is a melody where every note signifies optimal resource utilization, continuous improvement, and unyielding commitment to quality and efficiency. TPS wasn’t merely about manufacturing cars. It was a philosophy, a mindset that ensured that every resource was utilized optimally, that every process was continuously refined, and that every product resonated with the essence of quality and excellence. It was a system where productivity was not a goal but a journey, a continuous, unending journey towards organizational excellence and customer satisfaction.
Principle 2: Eliminate Waste – A Symphony of Efficiency and Mindfulness in Kaizen
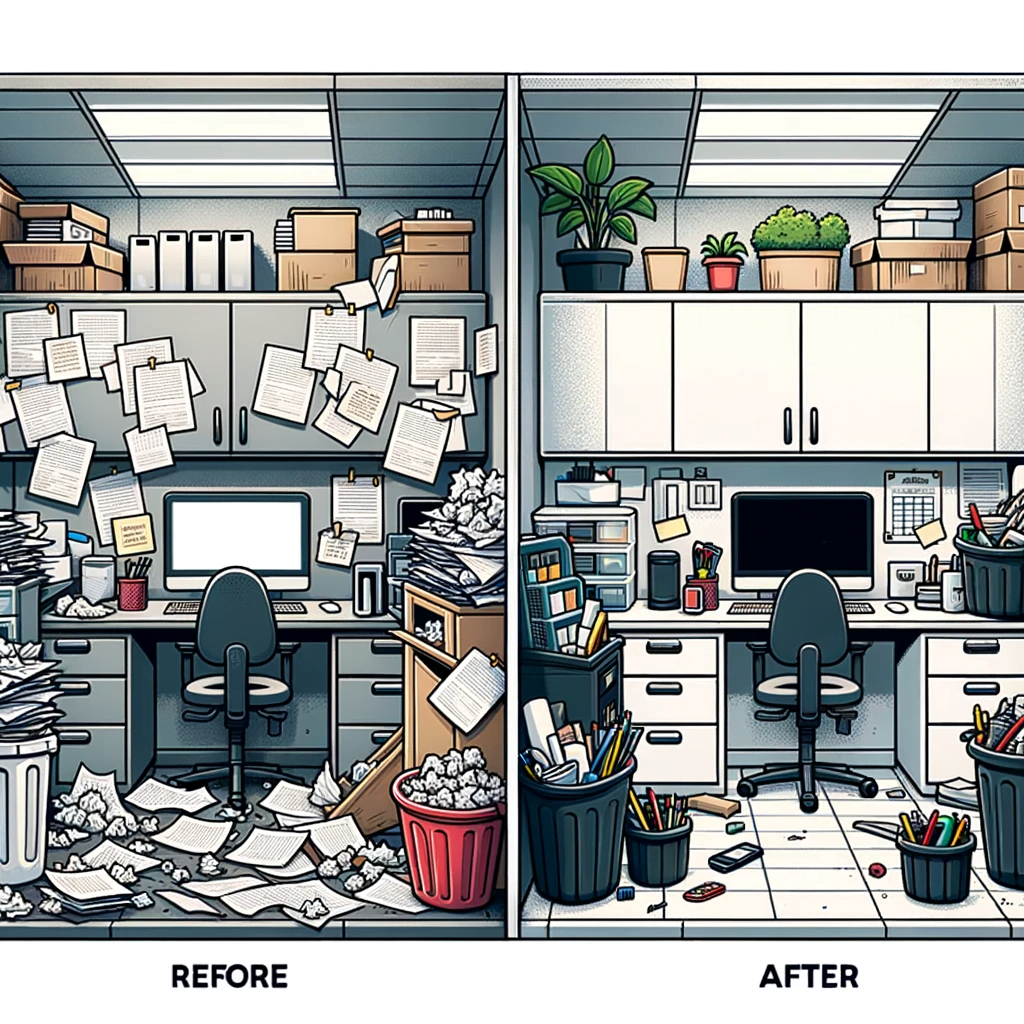
Identifying Waste: The Unseen Culprit of Inefficiency
In the harmonious journey through the “10 Principles of Kaizen,” the second principle gently caresses the essence of eliminating waste. Picture a serene garden, where every wilted leaf is gently removed, ensuring that every bud blossoms and every plant thrives. Identifying waste in the organizational garden is akin to spotting these wilted leaves. It’s about recognizing the unseen, the subtle culprits that hinder growth, obstruct blossoming, and impede the flourishing of organizational processes. It’s about ensuring that every resource, every effort, and every action is utilized to its fullest, ensuring a lush, vibrant, and thriving organizational landscape.
Mitigating Waste: A Gentle Embrace of Mindfulness and Efficiency
Eliminating waste isn’t merely about removal; it’s about prevention, about crafting a landscape where waste has no place to take root. It’s about ensuring that every process, every action, and every resource is optimized, ensuring that waste is not just removed but is prevented at its source. Mitigating waste is about crafting a symphony where every note, every beat, and every melody is in harmony with the organizational objectives, ensuring a melody of efficiency, effectiveness, and sustainable growth.
Strategies and Techniques: Crafting a Waste-Free Landscape
In the real-world application of this principle, it’s about employing strategies and techniques that not only identify and eliminate waste but prevent its occurrence. Techniques such as the 5 Whys, which delve into the root cause of issues, ensuring that waste is identified at its source and eliminated. Strategies such as Just-In-Time, which ensures that resources are utilized optimally, preventing the waste of resources and ensuring a smooth, efficient, and waste-free operation. It’s about employing techniques and strategies that ensure that the organizational garden is not just free of waste but is also optimized for lush, vibrant, and sustainable growth.
Principle 3: Standardize – Crafting Consistency in the Kaizen Tapestry
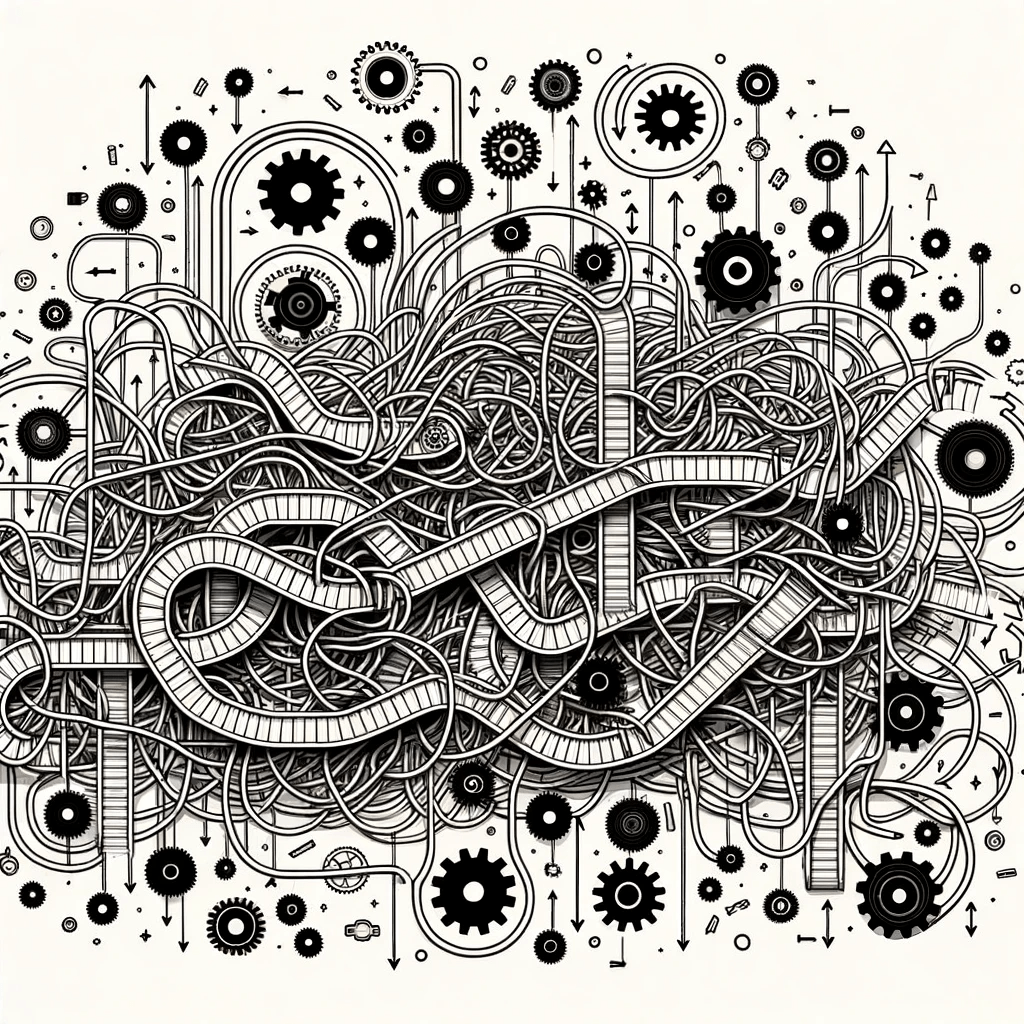
The Vitality of Standardization in Organizational Processes
Embarking further into the “10 Principles of Kaizen,” the third principle, Standardize, emerges as a gentle guide through the realms of consistency and uniformity in organizational processes. Picture a symphony, where every musician, every instrument, and every note is in harmonious alignment, crafting a melody that resonates with every listener. Standardization in organizational processes is akin to this harmony, ensuring that every action, every process, and every outcome is consistent, predictable, and in alignment with the organizational objectives. It’s about crafting a melody where every note, every beat, and every rhythm is in harmonious synchronization, ensuring a melody of efficiency, predictability, and quality.
Navigating Through the Essence of Standardization
Standardization isn’t merely about consistency; it’s about crafting a landscape where every process, every action, and every outcome is predictable, reliable, and efficient. It’s about ensuring that the organizational symphony is not just melodious but is also consistent, ensuring that every rendition, every performance, and every outcome is in alignment with the organizational objectives. It’s about crafting a melody that is not just harmonious but is also reliable, ensuring that every note played resonates with the essence of quality, efficiency, and customer satisfaction.
Strategies for Implementing Standardization
In the practical arena, implementing standardization involves crafting strategies that ensure that every process is not just efficient but is also consistent and predictable. Techniques such as Process Mapping, which ensures that every process is documented, analyzed, and optimized, ensuring that every step, every action, and every outcome is in alignment with the organizational objectives. Strategies such as SOPs (Standard Operating Procedures), which ensure that every process, every action, and every task is performed consistently, ensuring that every note played in the organizational symphony is in harmonious alignment with the melody of quality, efficiency, and customer satisfaction.
Principle 4: Utilize Employee Potential – Harmonizing Individual Growth with Organizational Success in Kaizen
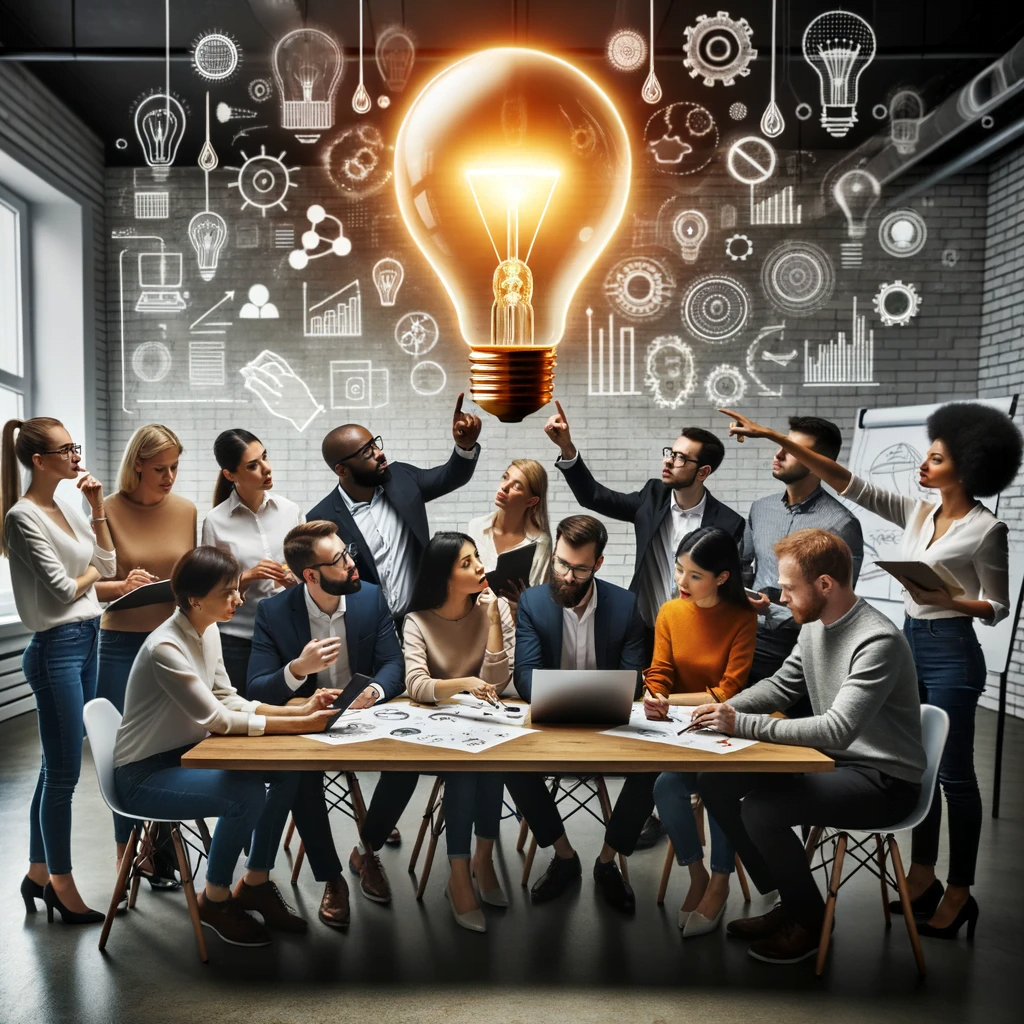
Engaging Employees: The Melody of Collective Growth
As we gently tread through the “10 Principles of Kaizen,” the fourth principle, Utilize Employee Potential, unfolds as a melody that harmonizes individual growth with organizational success. Imagine a symphony where every musician is not just performing but is also contributing to the composition, ensuring that the melody is not just harmonious but is also evolving, growing, and blossoming with every note. Engaging employees in the Kaizen journey is akin to this evolving melody, ensuring that every individual is not just performing their role but is also contributing to the continuous improvement and growth of the organizational symphony.
The Symphony of Employee Involvement
Involving employees in improvement processes isn’t merely about participation; it’s about ensuring that every individual is an integral part of the organizational growth and improvement journey. It’s about ensuring that every note played by every musician is in harmony with the organizational objectives, ensuring a melody that is not just harmonious but is also continuously improving and evolving. It’s about crafting a symphony where every musician is not just a performer but is also a composer, contributing to the continuous improvement, evolution, and success of the organizational melody.
Benefits: Crafting a Melody of Success and Satisfaction
The benefits of employee involvement in the Kaizen journey are manifold. It’s not just about improving processes and enhancing efficiency; it’s about ensuring that every individual is an integral part of the organizational journey, ensuring that they are not just performers but are also contributors to the organizational success story. It’s about ensuring that the organizational symphony is not just melodious but is also a melody where every musician is satisfied, engaged, and is an integral part of the success story. It’s about crafting a melody that resonates with success, satisfaction, and continuous improvement.
Principle 5: Quality Management – Weaving a Tapestry of Excellence in Kaizen

Ensuring Quality: The Gentle Whisper of Excellence in Every Process
As we gracefully dance through the “10 Principles of Kaizen,” principle five, Quality Management, unfolds like a gentle whisper of excellence, permeating through every process, every action, and every outcome in the organizational journey. Imagine a tapestry, where every thread, every color, and every pattern is meticulously crafted, ensuring a masterpiece that is not just visually stunning but is also durable, reliable, and timeless. Ensuring quality in every process is akin to crafting this tapestry, ensuring that every action, every process, and every outcome is not just efficient but is also reliable, consistent, and meets the highest standards of excellence.
The Art and Science of Quality Management
Quality management is not just about ensuring excellence; it’s about crafting a landscape where excellence is the norm, where every process, every action, and every outcome is meticulously crafted to meet the highest standards. It’s about ensuring that the organizational tapestry is not just visually stunning but is also a masterpiece of reliability, consistency, and excellence. It’s about crafting a landscape where every thread, every pattern, and every color is in harmonious alignment with the organizational objectives, ensuring a tapestry that is not just a visual masterpiece but is also a testament to the excellence, reliability, and quality of the organization.
Techniques: Crafting Excellence in Every Thread
In the practical realm, quality management involves employing techniques that ensure that every process, every action, and every outcome is of the highest quality. Techniques such as Total Quality Management (TQM), which ensures that every process is optimized for quality, and Six Sigma, which ensures that every process is as defect-free as possible, ensuring that the organizational tapestry is not just a visual masterpiece but is also a testament to the reliability, consistency, and quality of the organization.
Principle 6: Utilize Technology – Illuminating the Path of Continuous Improvement with Technological Brilliance
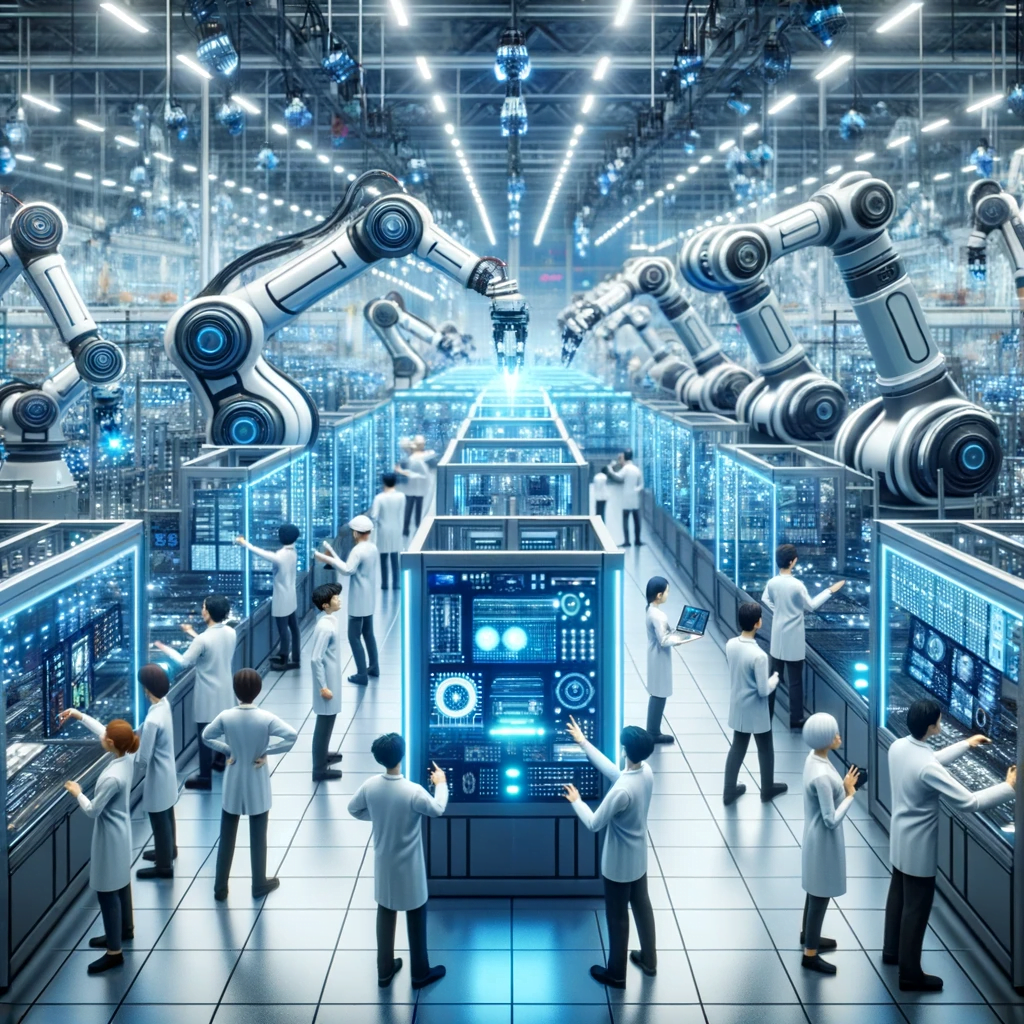
Leveraging Technology: A Beacon of Progress in the Kaizen Journey
Embarking further into our exploration of the “10 Principles of Kaizen,” principle six, Utilize Technology, emerges as a beacon, illuminating the path of continuous improvement with the brilliance of technological advancements. Picture a lighthouse, steadfastly guiding ships through the darkest nights, ensuring safe passage through even the most treacherous of seas. Leveraging technology in the Kaizen journey is akin to this lighthouse, ensuring that the path of continuous improvement is not just efficient and effective but is also innovative, forward-thinking, and in harmonious alignment with the ever-evolving technological landscape.
The Symphony of Continuous Improvement and Technology
In the realm of Kaizen, utilizing technology is not just about adopting the latest tools and technologies; it’s about crafting a symphony where technology and continuous improvement are in harmonious alignment, ensuring a melody that is not just efficient and effective but is also innovative, forward-thinking, and capable of navigating through the ever-evolving technological seas. It’s about ensuring that the Kaizen journey is not just a path of continuous improvement but is also a journey of continuous innovation, evolution, and technological advancement.
Case Studies: Navigating through the Seas of Technological Advancement
In the practical world, numerous organizations have illuminated their path of continuous improvement with the brilliance of technology, ensuring a journey that is not just efficient and effective but is also innovative and forward-thinking. Companies like Toyota, with their innovative use of automation and robotics, and Amazon, with their utilization of advanced data analytics and machine learning, have showcased that the path of continuous improvement is not just a journey of efficiency and effectiveness but is also a journey of innovation, evolution, and technological brilliance.
Principle 7: Just-in-Time Production – Navigating Through the Intricacies of Timely Manufacturing
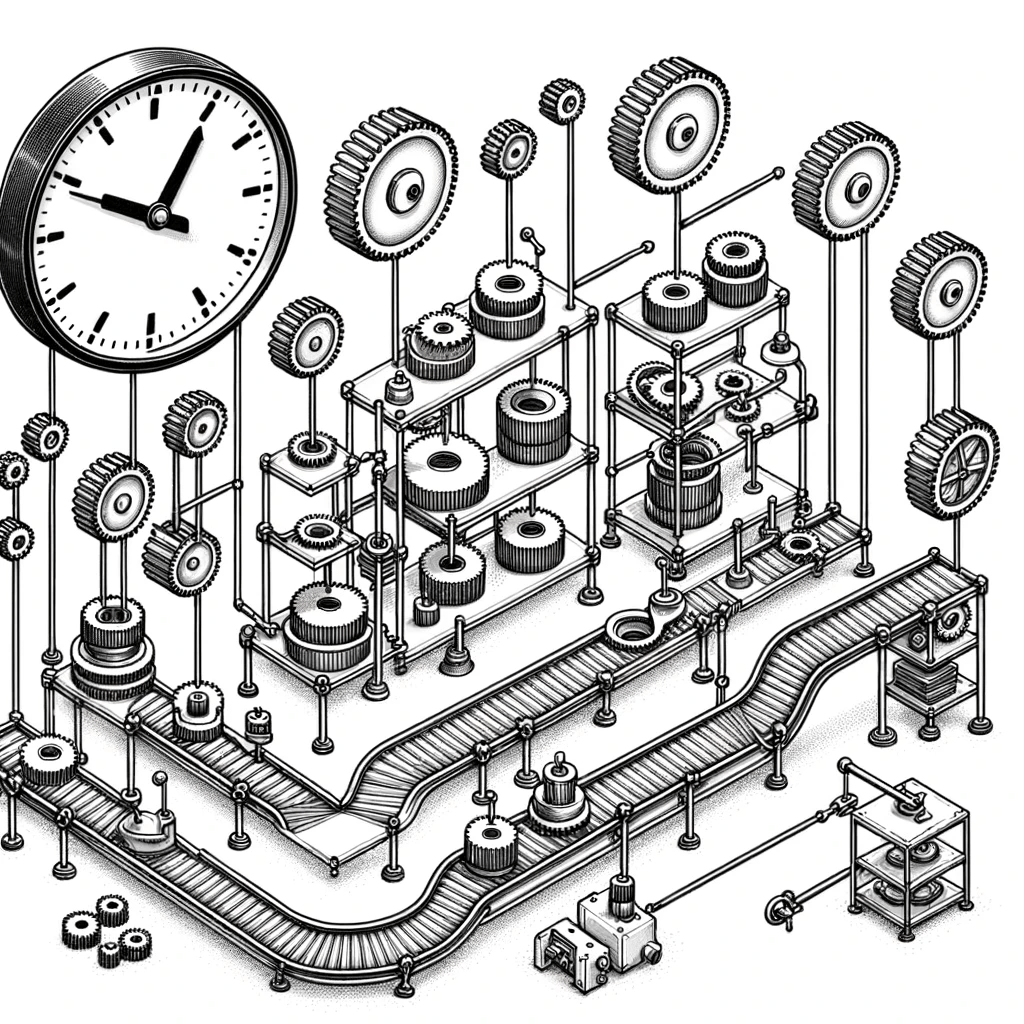
Understanding Just-in-Time (JIT) Production: A Synchronized Ballet of Processes
In the harmonious world of the “10 Principles of Kaizen,” the seventh principle, Just-in-Time Production, dances gracefully into the spotlight, orchestrating a synchronized ballet where every process, every action, and every piece of material is meticulously timed to ensure that production is not just efficient and effective, but is also timely, waste-free, and impeccably synchronized.
Just-in-Time Production, or JIT, is a philosophy that stands firm on the belief that production should be a ballet, where every movement, every process, and every piece of material is meticulously choreographed to ensure that everything is produced, moved, and created at precisely the right time, ensuring a production process that is not just efficient and effective, but is also free from the burdens of excess inventory, delayed processes, and wasteful practices.
Implementing JIT: A Journey Through Timely and Efficient Production
Embarking on the journey of JIT is akin to choreographing a ballet, where every movement, every process, and every piece of material must be meticulously planned, timed, and executed to ensure a performance that is not just beautiful but is also free from the chaos of missteps, delays, and disruptions. Implementing JIT requires a meticulous understanding of every process, every material, and every movement, ensuring that everything is produced, moved, and created at precisely the right time, ensuring a production process that is not just efficient and effective but is also harmoniously synchronized and free from the burdens of excess, delay, and waste.
Advantages and Challenges: Navigating Through the Seas of JIT
While JIT offers a sea of advantages, ensuring a production process that is efficient, effective, and free from the burdens of excess and waste, it also presents a sea of challenges, requiring organizations to navigate through the intricacies of meticulous planning, precise timing, and impeccable execution. The advantages, from reduced inventory costs to enhanced efficiency, and the challenges, from the need for precise timing to the requirement for flawless execution, must be navigated with meticulous care, ensuring a journey that is not just efficient and effective but is also capable of navigating through the seas of challenges that JIT presents.
Principle 8: Systematic Problem Solving – Crafting Solutions Through Methodical Approaches
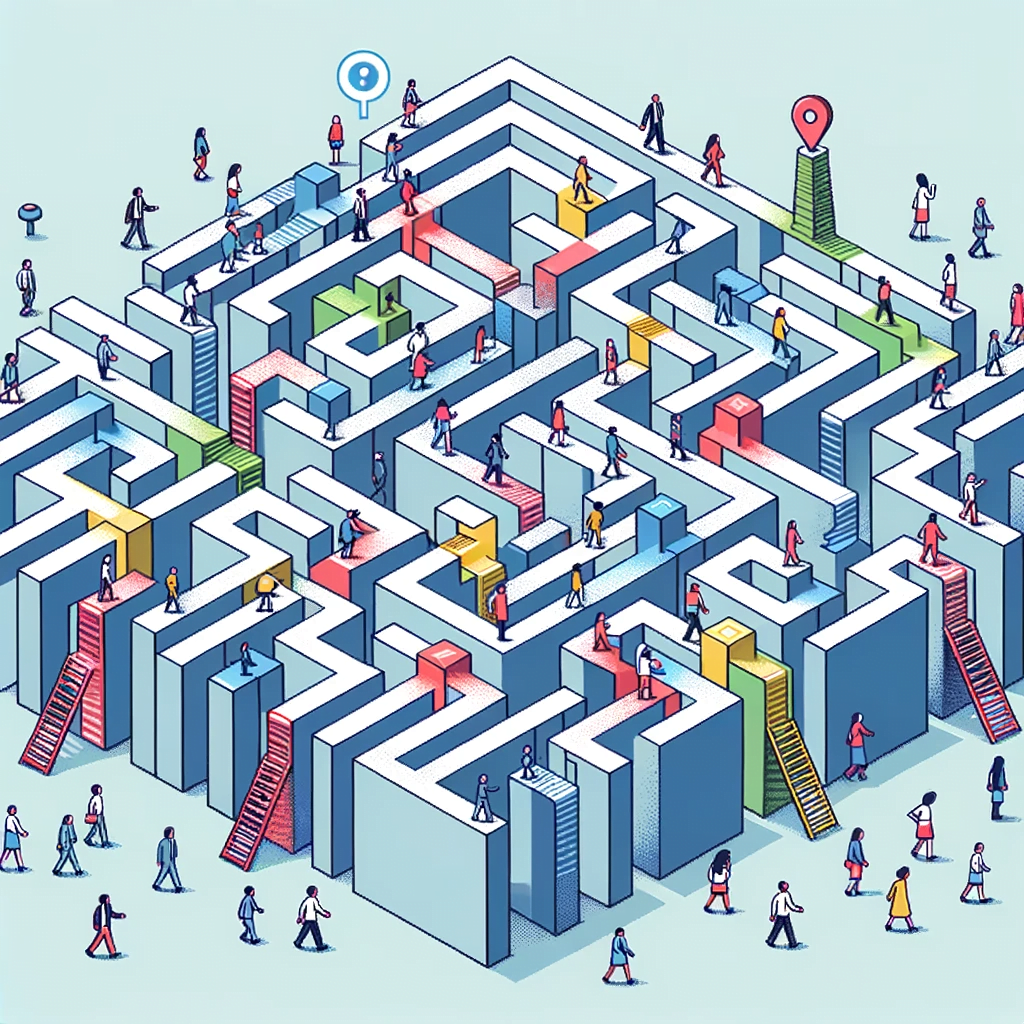
Techniques for Identifying and Solving Problems: A Methodical Approach to Challenges
In the realm of the “10 Principles of Kaizen,” Principle 8, Systematic Problem Solving, emerges as a beacon of strategic thinking and methodical approaches, guiding organizations through the often-turbulent seas of challenges, issues, and problems with a calm, structured, and systematic approach.
Systematic Problem Solving is not merely a principle; it’s a philosophy that embraces the belief that every problem, every challenge, and every issue can be solved with a methodical, structured, and systematic approach. It’s a belief that sees problems not as insurmountable obstacles but as opportunities for improvement, innovation, and development, guiding organizations through the process of identifying, analyzing, and solving problems with a calm, structured, and systematic methodology.
Case Studies on Effective Problem Solving: Stories of Triumph Over Challenges
Embarking on a journey through various organizations and their stories of triumph over challenges, we find a common thread – a methodical, structured, and systematic approach to problem-solving that has not only enabled them to navigate through challenges but has also empowered them to turn these challenges into opportunities for improvement, innovation, and development.
From manufacturing giants who have turned production challenges into opportunities for optimization, to service organizations that have transformed customer issues into chances for enhancement and improvement, the stories of triumph are not just numerous but are also varied, showcasing the versatility, applicability, and effectiveness of systematic problem-solving in various contexts, scenarios, and situations.
Principle 9: Adopting a Long-term Philosophy – Navigating the Balance Between Present and Future
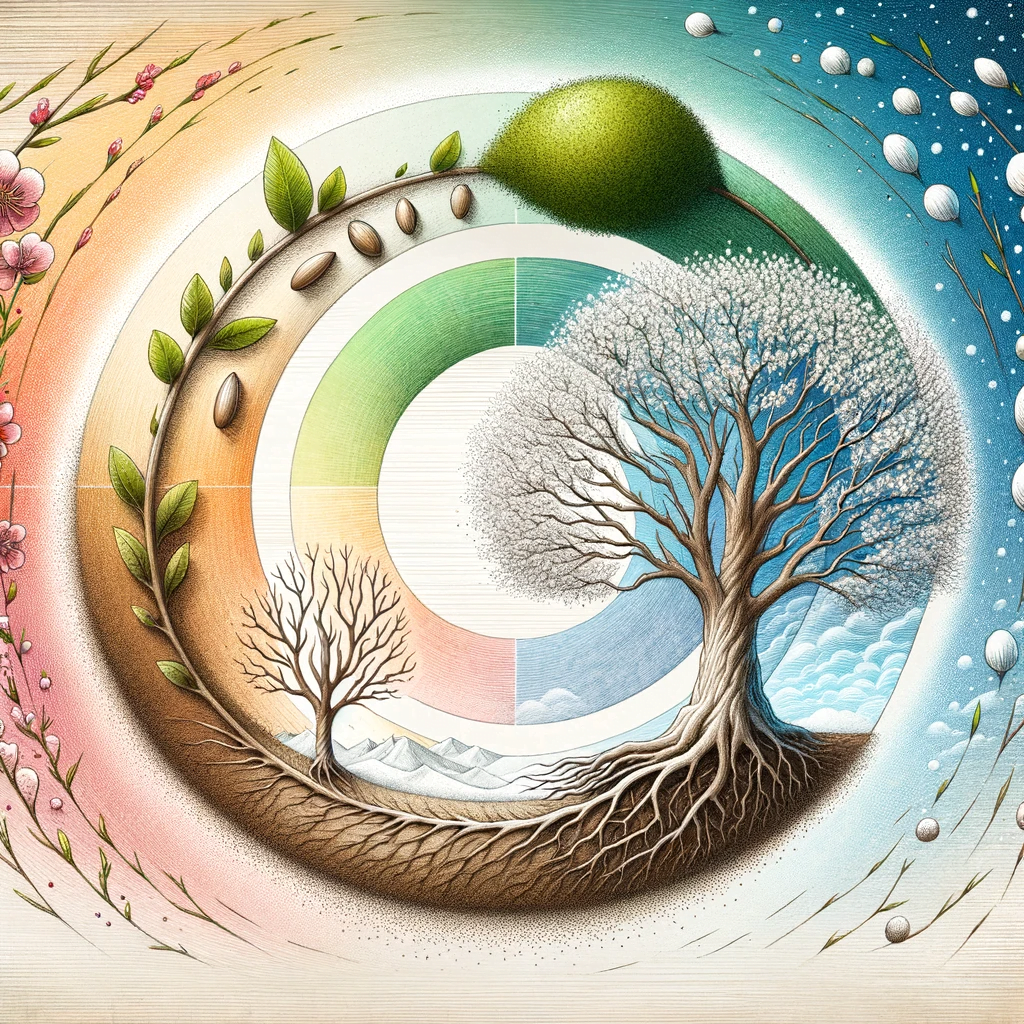
Balancing Short-term Goals with Long-term Vision: A Delicate Dance Towards Success
In the profound journey through the “10 Principles of Kaizen,” Principle 9, Adopting a Long-term Philosophy, stands out as a testament to the delicate balance between the immediacy of short-term goals and the foresight of a long-term vision. It’s a principle that doesn’t merely advocate for a vision that spans across decades but also emphasizes the importance of not losing sight of the immediate, short-term goals that pave the way towards that vision.
Adopting a long-term philosophy is not just about having a vision; it’s about ensuring that every short-term goal, every immediate objective, and every quick win is a step towards realizing that vision. It’s about ensuring that the pursuit of immediate results does not derail the journey towards long-term success, and that every short-term goal is a building block towards the realization of the long-term vision.
Strategies for Long-term Success: Crafting a Future Through Strategic Thinking
Navigating through the myriad of strategies for long-term success, we find a common theme – a strategic, structured, and systematic approach that ensures every immediate action, every short-term goal, and every quick win is not just a standalone achievement but is a step towards the realization of a long-term vision.
From organizations that have successfully navigated through immediate challenges without losing sight of their long-term vision, to businesses that have turned immediate wins into stepping stones towards future success, the strategies for long-term success are as varied as they are numerous, showcasing the versatility and applicability of adopting a long-term philosophy in various contexts and scenarios.
Principle 10: Continuous Learning – Fostering a Culture of Endless Growth and Improvement
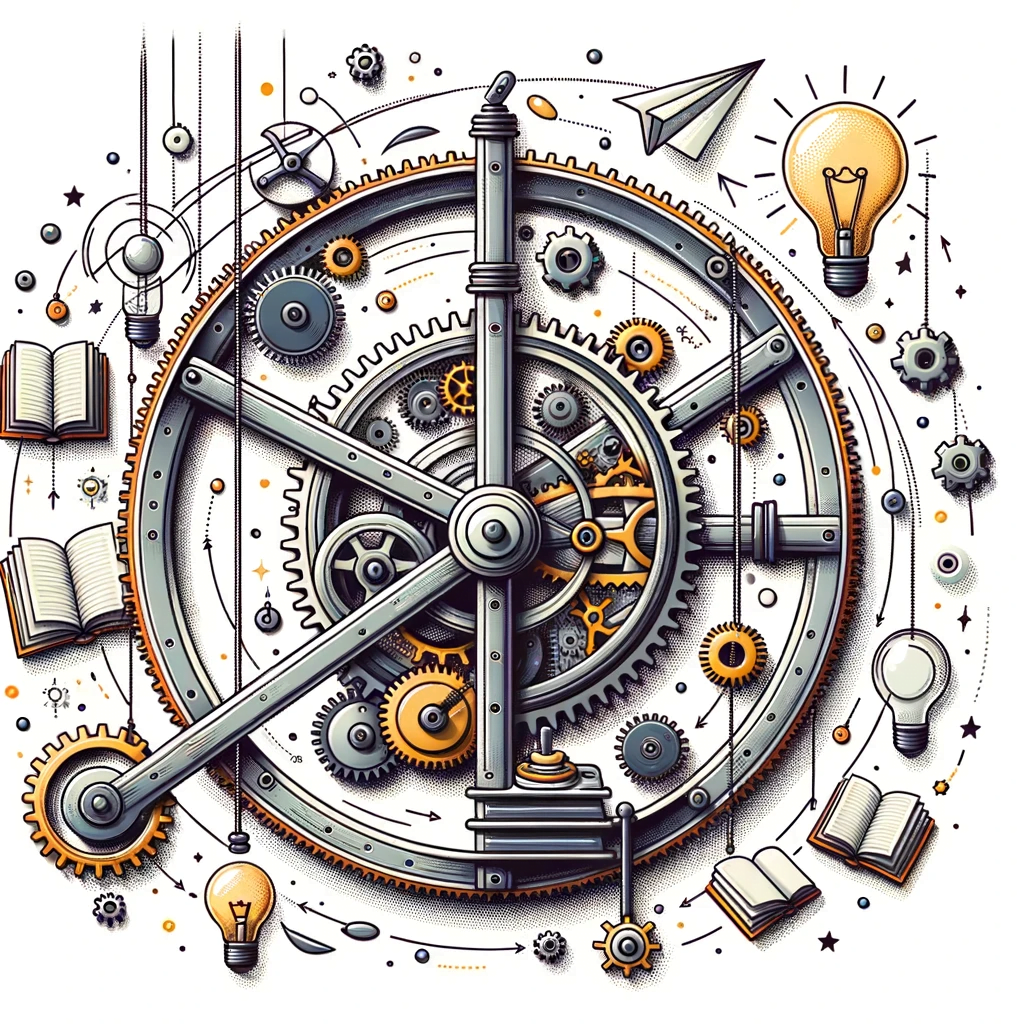
Promoting a Learning Culture: The Heartbeat of Continuous Improvement
Embarking on the final leg of our journey through the “10 Principles of Kaizen,” Principle 10, Continuous Learning, emerges as a beacon of perpetual growth and improvement. It’s not merely a principle; it’s a culture, a mindset, and a philosophy that permeates every layer of an organization, ensuring that learning and improvement are not sporadic, but continuous, consistent, and perpetual.
In the realm of Kaizen, continuous learning is not confined to merely acquiring new knowledge or skills. It’s about fostering a culture where learning is embedded into the very fabric of the organization, where every individual, irrespective of their role or position, is a perpetual learner, continuously seeking ways to improve, grow, and evolve.
Strategies for Continuous Learning and Improvement: Navigating the Path of Perpetual Growth
Navigating through the myriad of strategies for continuous learning and improvement, we find a common theme – a structured, systematic, and strategic approach that ensures every individual is not just a passive recipient of knowledge but an active participant in the learning process.
From organizations that have successfully embedded a culture of continuous learning to businesses that have transformed learning from a sporadic event to a continuous journey, the strategies for continuous learning and improvement are as varied as they are numerous, showcasing the versatility and applicability of adopting a continuous learning philosophy in various contexts and scenarios.
Implementing Kaizen in Your Organization: A Step-by-Step Guide to Adopting a Philosophy of Continuous Improvement
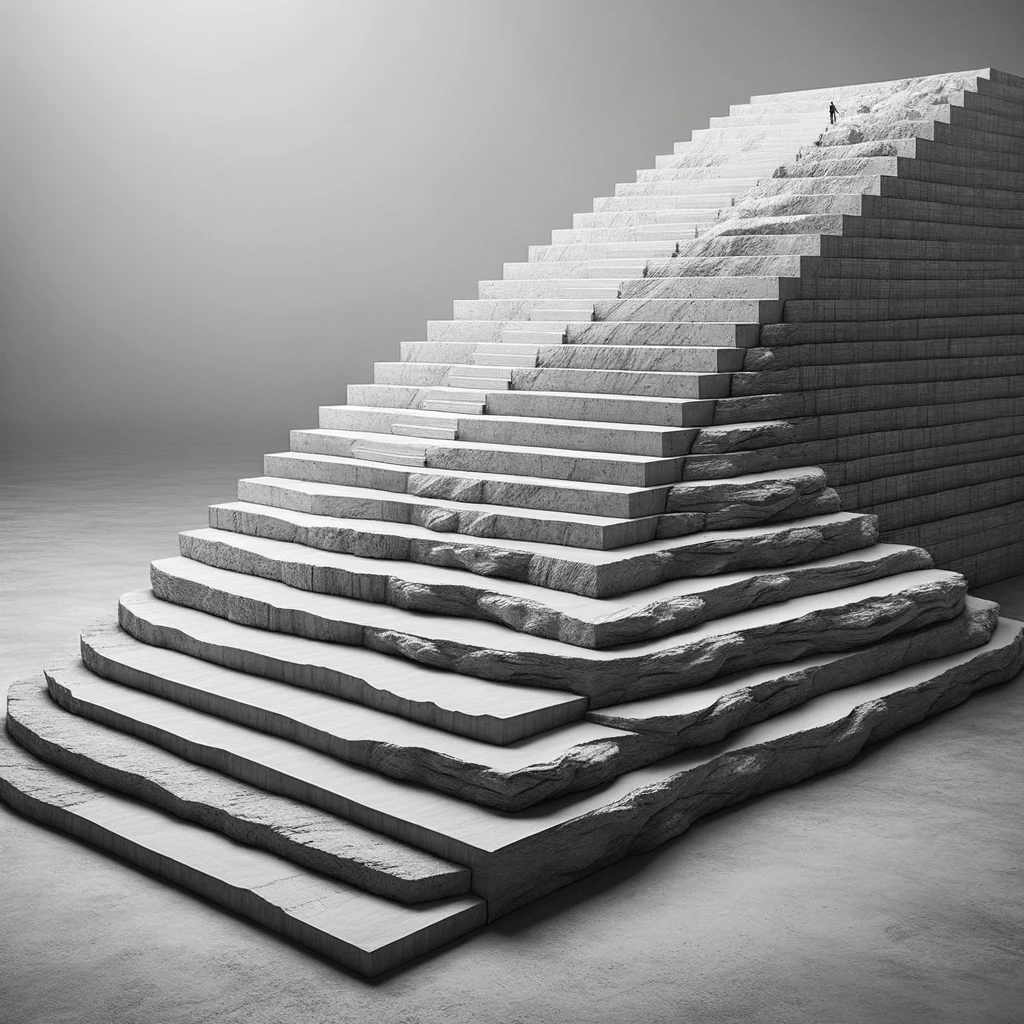
Steps to Adopt Kaizen Principles: Embarking on a Journey of Continuous Improvement
Embarking on the journey of implementing the “10 Principles of Kaizen” in your organization is akin to planting a seed of continuous improvement, nurturing it with the right strategies, and watching it grow and flourish, permeating every layer of the organization with a culture of perpetual learning, growth, and improvement.
- Understanding Kaizen: Begin by understanding and embracing the philosophy of Kaizen, ensuring that it is not just adopted at an organizational level but understood and embraced by every individual.
- Training and Development: Invest in training and development, ensuring that every individual is not just aware of Kaizen but is also equipped with the knowledge and skills to implement it.
- Implementing Principles: Begin the implementation of the principles, ensuring that they are not just adopted in theory but are also implemented in practice.
- Continuous Monitoring: Ensure continuous monitoring and evaluation of the implementation, ensuring that the principles are not just implemented but are also yielding the desired results.
Overcoming Challenges in Implementation: Navigating Through the Hurdles with Grace and Strategy
Implementing Kaizen is not without its challenges. From resistance to change to hurdles in implementation, the journey is fraught with challenges that need to be navigated with grace, strategy, and foresight.
- Resistance to Change: Address resistance to change by ensuring transparent communication, involving every individual in the process, and ensuring that they are not just passive recipients of change but active participants in it.
- Implementation Hurdles: Navigate through implementation hurdles by ensuring a structured, systematic, and strategic approach to implementation, ensuring that every step, no matter how small, is a step in the right direction.
Measuring Success and Continuous Improvement: Ensuring that the Journey Does Not End
The journey of Kaizen does not end with implementation. It is a continuous journey of improvement, where success is not just measured by the implementation of the principles but by the continuous improvement and growth that they yield.
- Measuring Success: Success is measured not just by the implementation of the principles but by the tangible and intangible benefits that they yield, from improved processes and performance to a culture of continuous improvement and learning.
- Continuous Improvement: Ensure that the journey of improvement does not end, that the principles of Kaizen are not just implemented but are also continuously improved upon, ensuring that the organization does not just grow but also evolves.
Case Studies: Success Stories of Kaizen Implementation
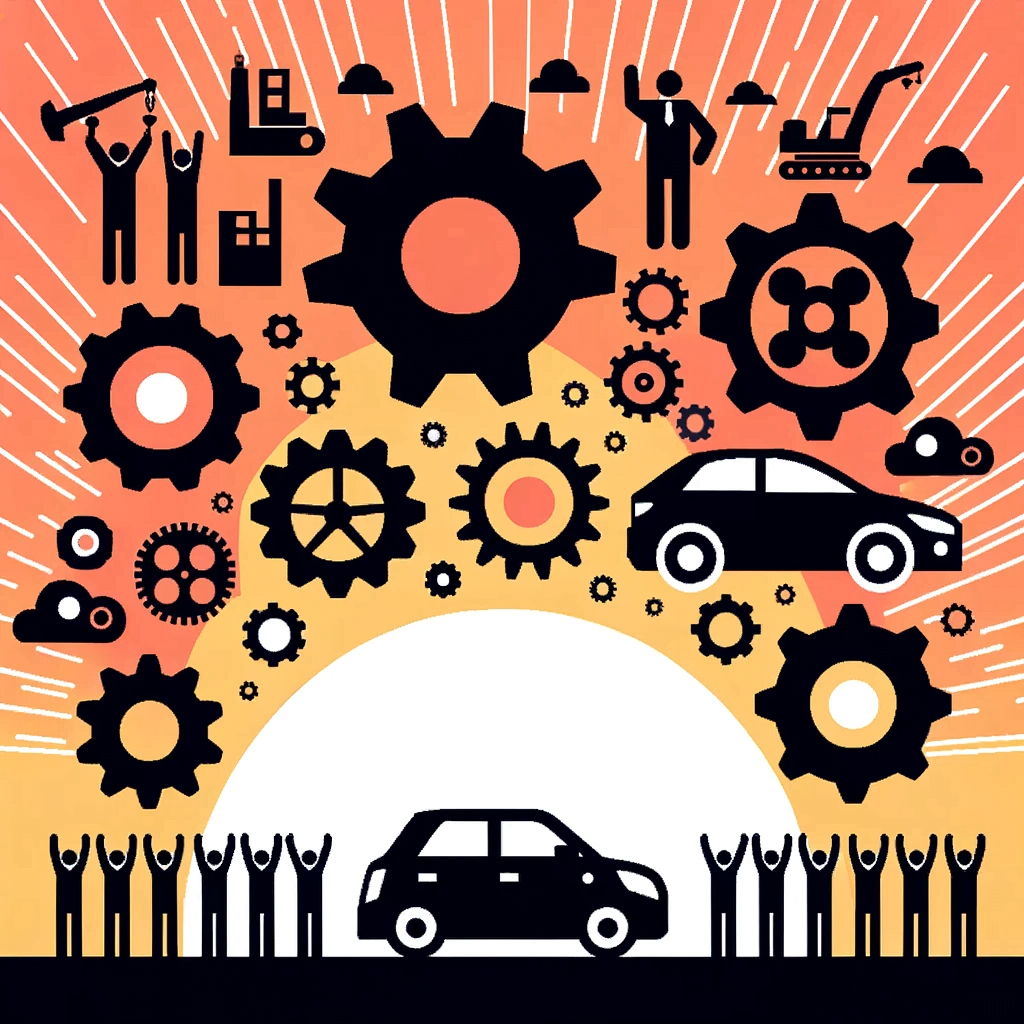
Toyota: The Birthplace of Kaizen
When we delve into the realm of continuous improvement and lean manufacturing, the story of Toyota stands out, gleaming with the principles of Kaizen at its core. Toyota, the Japanese automotive giant, didn’t just implement the “10 Principles of Kaizen”; it was the birthplace of this transformative philosophy.
The Toyota Production System (TPS), which is deeply embedded with Kaizen, revolutionized its operational efficiency, quality, and productivity. The principle of ‘Genchi Genbutsu’ or ‘Go and See’ was not merely a strategy but became the culture, where problems were not solved in boardrooms but on the shop floors where they occurred. Toyota’s success is not just in its high-quality, efficient production but in creating a culture where every employee is an active participant in continuous improvement.
Other Notable Companies Successfully Implementing Kaizen
The ripples of Kaizen have touched various shores and industries, transforming organizational cultures and operational efficiencies.
- Lockheed Martin: The global aerospace, defense, and security giant, Lockheed Martin, embraced Kaizen to enhance its production and operational efficiency. Through Kaizen events, they managed to significantly reduce waste, improve quality, and enhance their delivery times, ensuring that the principles of continuous improvement were not just implemented but became a part of their organizational DNA.
- Ford Motor Company: Ford’s adoption of Kaizen principles has been pivotal in streamlining its processes and enhancing quality. By focusing on continuous improvement and involving every employee in the process, Ford managed to not just improve its operational efficiency but also enhance its product quality and customer satisfaction.
- Mayo Clinic: The implementation of Kaizen isn’t limited to manufacturing. Mayo Clinic, a renowned name in healthcare, adopted Kaizen to enhance patient care and improve operational efficiency. Through continuous improvement, they managed to enhance patient experiences, reduce waiting times, and improve healthcare delivery, showcasing that Kaizen can transcend industries and be successfully implemented in various domains.
Challenges and Criticisms of Kaizen
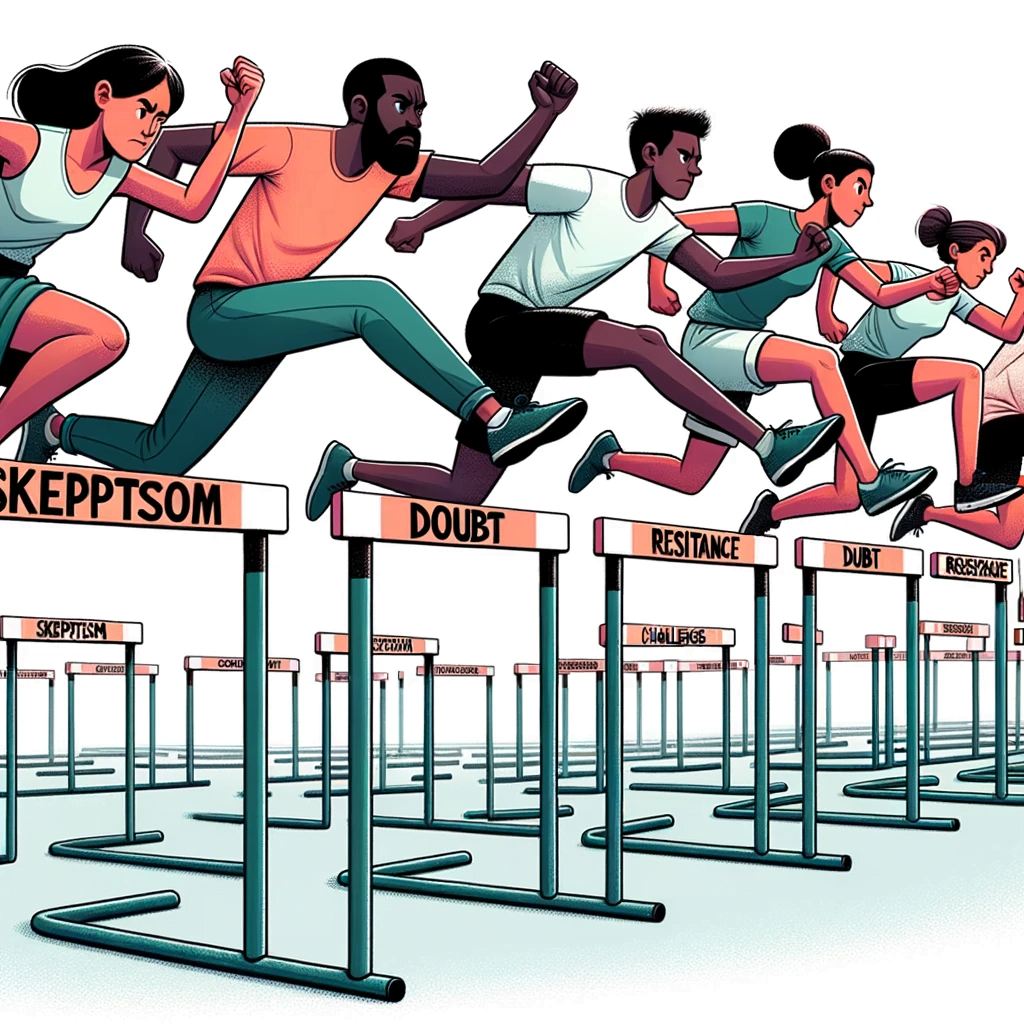
Common Criticisms and Counterarguments
Kaizen, despite its widespread acclaim and global implementation, has not been immune to criticisms. One common critique revolves around its applicability and effectiveness across diverse organizational cultures and structures. Detractors argue that the “10 Principles of Kaizen” may be deeply rooted in Japanese work ethics and may not seamlessly translate to other cultural contexts.
Moreover, the constant pursuit of incremental improvements, a core tenet of Kaizen, is sometimes seen as a potential hindrance to radical innovations and shifts that might be necessary in certain volatile markets. Critics suggest that the meticulous and continuous small improvements might divert attention from larger, more disruptive innovations and strategies.
However, proponents of Kaizen argue that the philosophy is not rigid but is adaptable and can be molded to fit various organizational cultures and needs. They emphasize that while Kaizen advocates for continuous, incremental improvements, it does not inherently oppose or restrict breakthrough innovations.
Addressing and Overcoming Challenges
Addressing the challenges and criticisms of Kaizen involves a nuanced understanding and flexible implementation of its principles. It’s pivotal to ensure that while the organization embarks on the journey of continuous improvement, it does not lose sight of the larger strategic picture and potential opportunities for disruptive innovations.
Organizations can overcome these challenges by fostering a Kaizen culture that is not just focused on incremental improvements but is also receptive to larger, transformative changes when needed. This involves maintaining a delicate balance between adhering to the principles of continuous improvement while remaining agile and open to significant shifts and innovations.
Moreover, ensuring that the implementation of Kaizen is adapted to the unique cultural and structural nuances of the organization, rather than adopting a one-size-fits-all approach, is crucial in addressing and mitigating common criticisms and challenges.
Conclusion: Embracing the Continuous Journey with Kaizen

Summarizing Key Takeaways
In our exploration of the “10 Principles of Kaizen,” we’ve navigated through a journey that encapsulates the essence of continuous improvement, from understanding its foundational principles to exploring its real-world applications and criticisms. Kaizen isn’t merely a methodology; it’s a philosophy that permeates every facet of an organization, advocating for an unwavering commitment to incremental advancements and holistic development.
The principles, ranging from eliminating waste to fostering a culture of quality management and systematic problem-solving, offer a roadmap to organizational excellence. They underscore the significance of adopting a mindset that views improvement not as a destination but as an ongoing journey.
Encouraging Continuous Improvement Beyond Kaizen
While Kaizen provides a robust framework for continuous improvement, it’s imperative to recognize that the journey towards organizational excellence extends beyond it. The spirit of Kaizen – the relentless pursuit of betterment – can be infused into every aspect of organizational life, transcending beyond methodologies and becoming ingrained in the organizational culture.
Embracing continuous improvement means perpetually seeking ways to enhance not only processes and systems but also fostering an environment that nurtures the professional and personal growth of its people. It’s about building a culture that doesn’t settle for the status quo but is perpetually driven by the quest for enhancement and evolution.
Final Thoughts and Encouragement for Implementation
Implementing Kaizen is not merely about adopting a set of principles; it’s about cultivating a mindset and culture that permeates through every layer of the organization. It’s a commitment to never settling, to perpetually striving for better, and to viewing challenges not as obstacles but as opportunities for growth and development.
As you embark on your Kaizen journey, remember that the path towards continuous improvement is not linear. It will be punctuated with challenges and opportunities, successes and setbacks. But it is this very journey, with its ebbs and flows, that fosters a resilient, adaptable, and thriving organization.
Embrace Kaizen, not just as a methodology, but as a philosophy that guides your organization towards a future of endless possibilities and continuous improvement. The journey might be perpetual, but every step forward is a step towards organizational excellence.